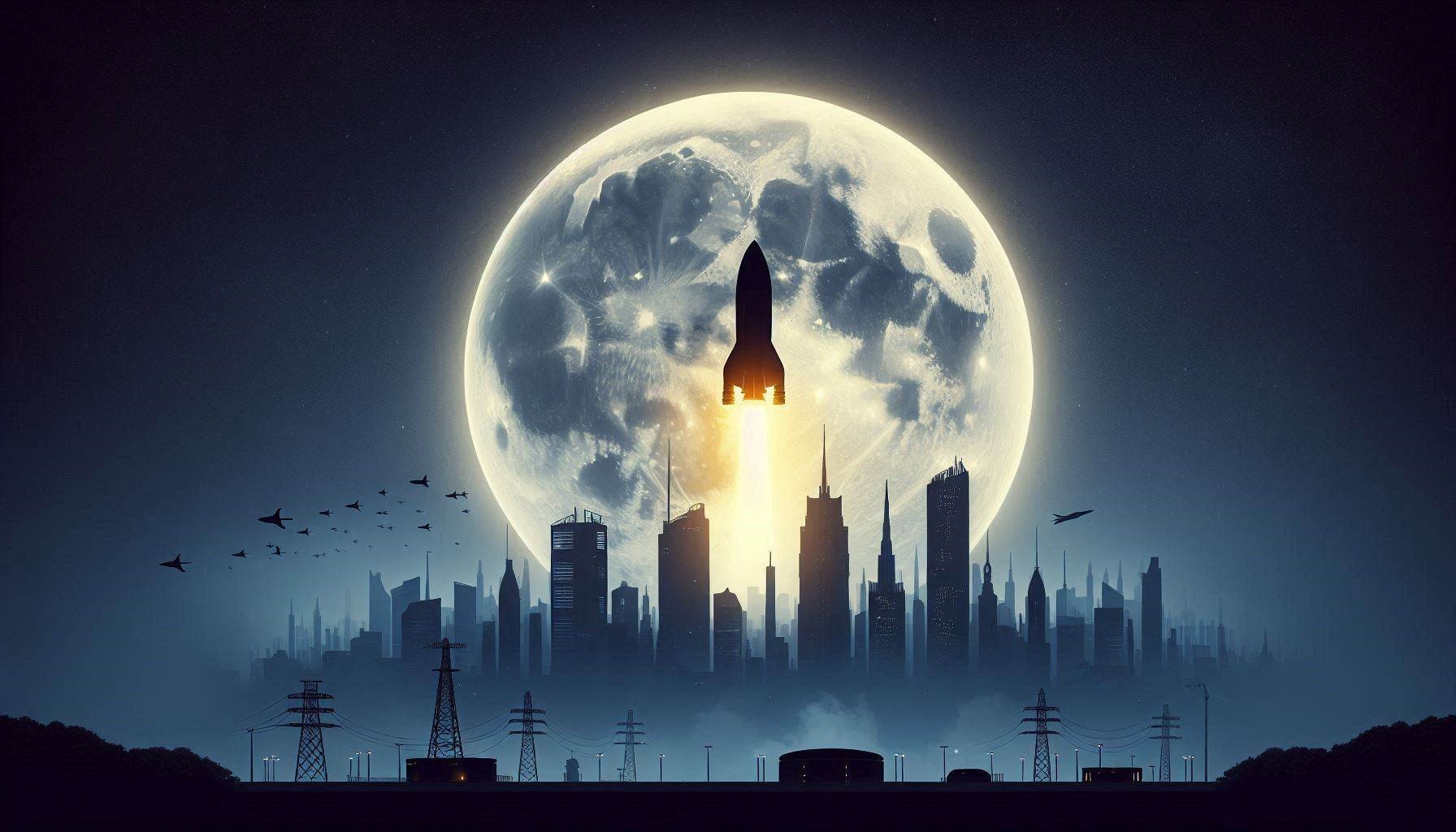
菊田一郎連載コラム
<物流ムーンショット>
Moonshots on Logistics
あるべき物流へ、勇気あるチャレンジを!
*ムーンショット*
前人未踏で非常に困難だが、達成できれば巨大なインパクトをもたらす壮大な計画や挑戦。
月を目指した、あのアポロ計画のように。
<MoonShots-4>
物流ロボットの力を全開!
機械を使いこなすカギは「人の情熱と執念」(その1)
目次
「マテハン」と「イントラロジスティクス」
ひと昔前まで、物流現場で自動化・省力化をする設備は、ひとまとめに「マテハン機器」と総称されていました。マテハンとは、マテリアル・ハンドリング(JIS規格で「荷役」の訳語になっている)の略で、モノを運び・扱うハンドリング作業の全体を指します。
それが1990年頃でしょうか。ヨーロッパ産業界の人たちは、「マテリアル・ハンドリング」というカテゴリの設備の機能・役割が進化し、旧来の言葉の範疇に収まりきらなくなっていることに気が付きました。ハードの自動化レベルが高まり、ソフトや情報システムの機能と範囲が広がり、新たな地平が拓かれていたからです。私の記憶では、これに「イントラロジスティクス」という名で新概念を与えたのは当時、世界最大のマテハン展示会「セマット」を開催していたハノーバーメッセの主催者、ドイツメッセ社ではなかったかと思います。今では他の欧米の展示会でもほぼ、「イントラロジスティクス」の呼び名が定着していますね。
でも日本では感覚的に消化しにくいせいか使われず、「マテハン」「物流機器」「倉庫自動化技術」などと雑然と呼ばれています。いずれにせよ、本コラム第1回で述べたムーンショット①物流センター自動化!――実現の主役が、これらの技術であることは間違いありません。
新カテゴリ? 「物流搬送ロボット」の3つの種類
ところがそこに、伝統的呼び名を押しのけて新たな市民権を獲得する勢いで登場したのが、「物流ロボット」ではないかと思います。大きく分けて「搬送」ロボットと「ハンドリング」ロボットがありますが、今回は「搬送」だけに絞って3種を見ていきます。
端緒を切ったのは何といっても、アマゾンが2012年にKIVA SYSTEMSを買収したことで一躍世界に知られた新技術「棚搬送ロボット(AGV)」でしょう。筆者は早くも2010年にアメリカの展示会NA取材で本機を初めて目にし、月刊誌の展示会レポートで「注目すべし!」と日本初の紹介記事を書いています。その時一緒に取り上げたのがノルウェーのロボット自動倉庫・AutoStoreであったことは、象徴的ですね。その後30年余にわたって世界の物流ロボット界をリードする両技術が、この前夜、同時多発的に誕生していたんですから。
①棚搬送ロボット(AGV)
さてこの「棚搬送ロボット」は、当時から床面に格子状に貼られた2次元シンボルを読み取って走るタイプのAGV(ガイド式無人搬送車)でした。昔のAGVは電磁ワイヤを床面に埋め込んだりしていたので、それに比べると簡易にはなりましたが、床面のガイドに従って走ること自体に変わりなく、私も初めは「普通のAGVじゃん!」と思っていました。しかし、使い方が違った(写真1、2)。
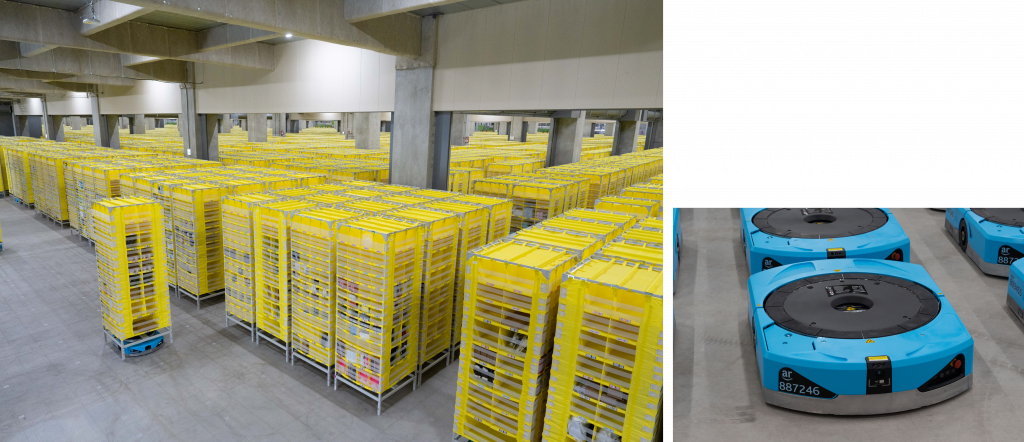
(AMAZON Newsroomより)
それまでは人が台車等を押して棚の間を歩き回り、必要な品目だけをピッキングする方式(Person To Goods)だったのを逆転し、モノが人のところにやってくる方式(Goods To Person/GTP)への革命的な変化=「歩かないピッキング」への進化が起きていたのです。それが報道されるようになると、棚の昇降機能など「ただのAGV」よりも一歩前進し、単体として自律的に駆動する姿がクローズアップされたことが、能動的イメージのある「物流ロボット」という呼称を獲得していく背景になったと感じます。
そもそも「マテハン」なんて一般の人は聞いたこともない言葉でしたよね。それが「物流ロボット」の謳い文句でテレビにも登場するようになって、「え? すごいじゃん!」と市井の人々の認識と愛着を深めるきっかけになったのは、大きな功績だと思います。今まさに注目の映画「ラストマイル」でも、その活躍の様子が描かれているというウワサです(筆者はまだ観てないけど、観に行く予定)。
②ロボット自動倉庫
AutoStoreは、商品を入れたプラコン(これを欧米ではビンと総称)を縦に十数段積み重ね前後左右も密集保管し、最上段を走り回るロボット台車が必要なビンを釣り上げてピッキングステーションに出庫することで、高密度保管と同時にGTP方式を実現しました。数十の台車が高速で、ぶつかり合うことなく見事に走り回ってビンをハンドリングする様子は、未来的な「ロボット自動倉庫」の一般名称を誰にも違和感のないものにしました。
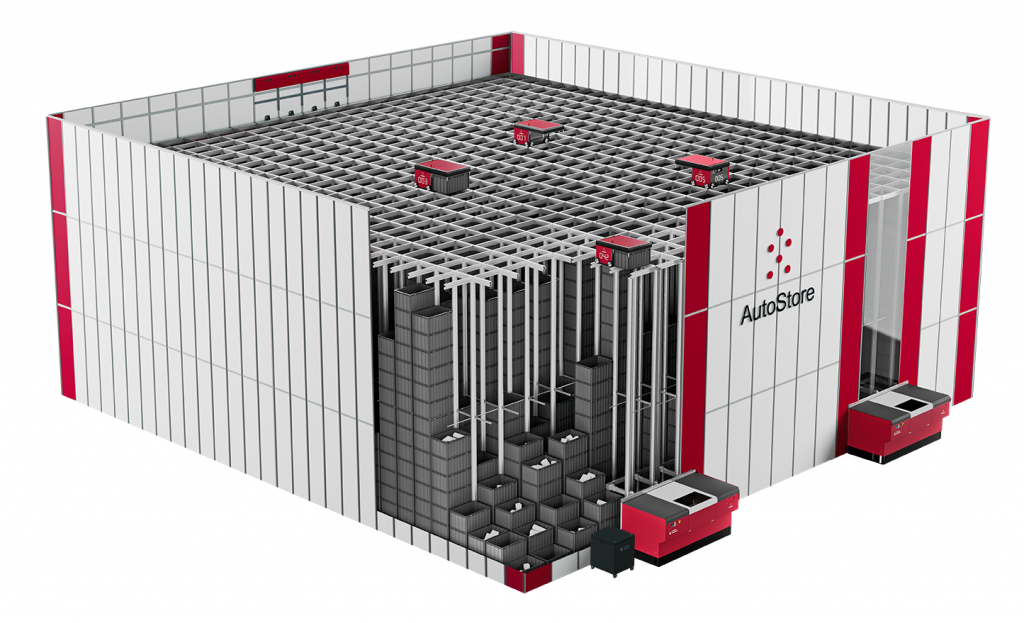
それ以前から自動倉庫の棚の間をシャトル台車が走行する、いわゆるシャトル自動倉庫が活躍してきました。ビンを高速入出庫することでAGV系に先立ち、人が歩かず定点ピックできる立派な「GTPシステム」を実現してきたことは、ご存じでしょうか?
その後、「シャトルロボットが庫外まで走り出て、ピッキングステーションまで自走してビンを入出庫する」タイプが登場、さらに加えて「走り出るロボットがクレーン不要で高層ラックの自律昇降機能も兼ね備えてしまう」という最新型ロボット自動倉庫にまで進化を遂げたのは、驚くべきことでした。その代表機種が仏EXOTEC社のSkypodで、国内でもファーストリテイリングが大量採用したのに続き、導入が拡大しています(写真4、5)。
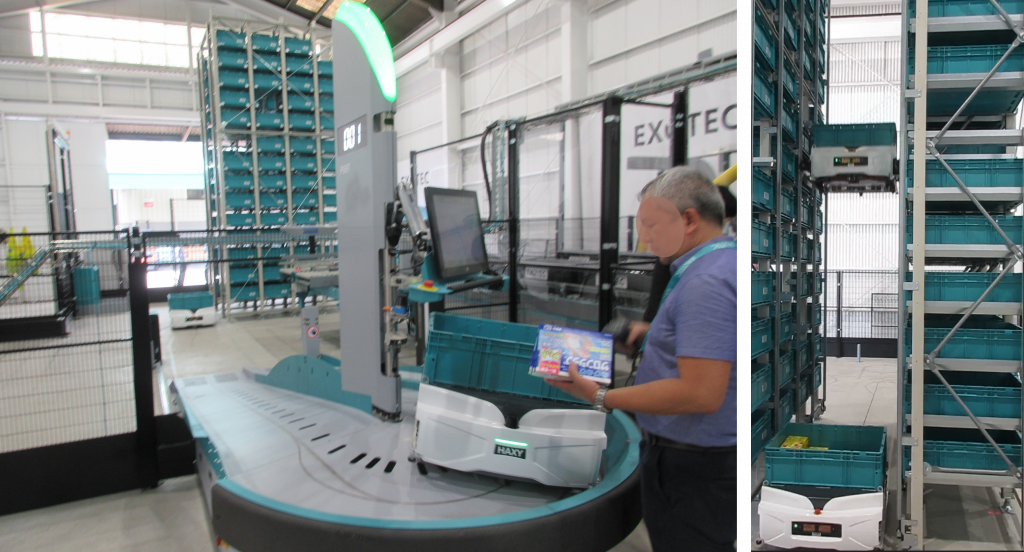
③自律型搬送ロボット(AMR)
走行に何らかのガイドを必要としていた従来型のAGVに対し、床面や壁面のガイド不要で、自らが持つ3Dデジタルマップデータをレーザセンサ、カメラなどで補足するSLAM方式により、ガイドレス走行と障害物回避も実現する自律型搬送ロボット(AMR)が近年、大きく普及してきました。技術進化の賜物であり、AGVと一線を画す自律性からロボットの称号を勝ち得ています。物流現場ではこのAMRが、従来は人がカートを押してラックの間を歩き回ってピックしていたカートピッキング作業における、「カート搬送を自動化する支援機器」として使われるようになりました。ムダに歩き回る距離を全部ではないけれど、半分以下とかに減らせるので、「余り歩かないピッキング」にできます(写真6)。
![写真6 AMRの導入例(アスクル日高AVC、ラピュタロボティクス製)
[同社ニュースリリースより]](https://logistics.shinwart.co.jp/wp-content/uploads/2024/09/%E2%98%85IMG_4402%EF%BC%8B-1024x616.jpg)
[同社ニュースリリースより]
物流ロボットの能力を全開するカギとは?(事例1/オルビス)
さあて、今回の<物流ムーンショット>は、そんな「物流ロボットの能力を全開!」すること。筆者があえてこのテーマを掲げた理由は、「能力を全開できてない物流ロボットが、実はかなり多いんじゃないか?」と心配しているからです。せっかく導入したロボットの力が発揮できてない? そんな勿体ないことがあるものか? でも……それじゃどうしたら、物流ロボットの能力を全開させられるのか?
筆者がこれまでに発見した2つの事例を通して、具体的に見ていきましょう。まず今回取り上げるのは、化粧品・健康食品のEC・店舗販売で知られるオルビス社。同社は2020年、埼玉県の東日本流通センターの通販専用出荷ラインに、330台ものAGVシステムを一挙導入しました。小型AGV(中国リビアオ社のt-Sort+を改造)がダブルループラインを雲霞の如く、大河のように流れていく様は、「小型ロボット大軍団」とでも言うか、じつに壮観です(写真7)。
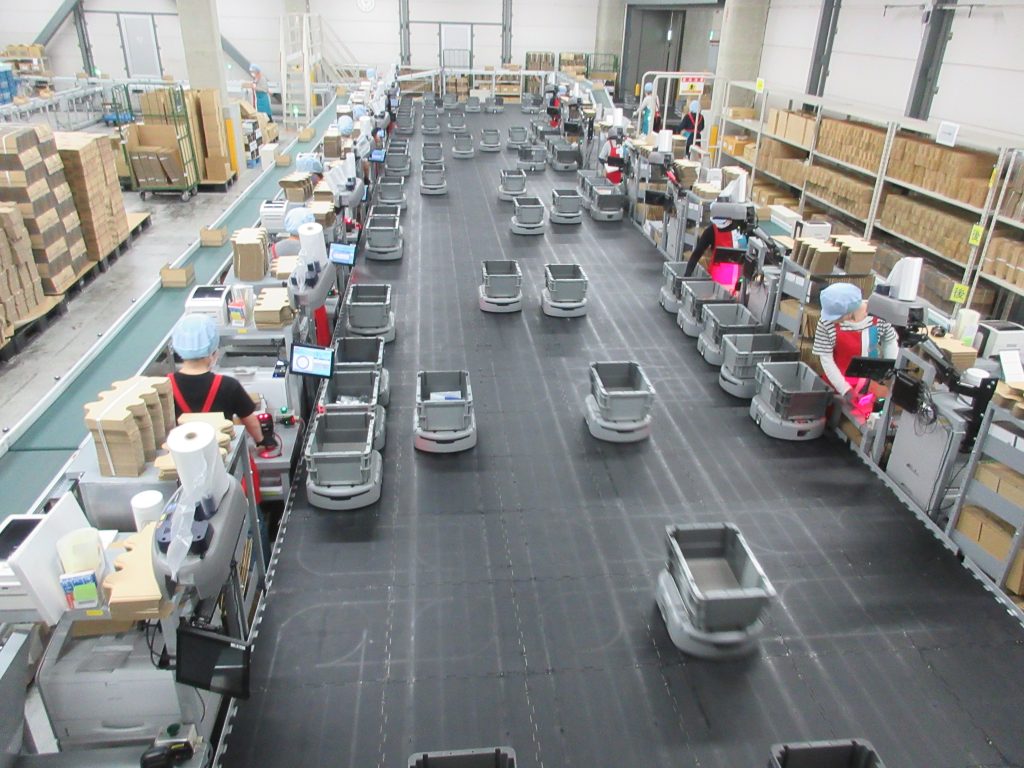
[筆者撮影]
1台に顧客の1オーダー(平均@8点)を割り当てたAGVは、周囲22か所のデジタルピッキングステーションのうち受注品のある場所だけに立ち寄り、ピック作業者が商品を棚からとってプラコンに投入。集め終わったら写真の反対側の下流にある34か所の梱包ステーションに届け、梱包作業者がバーコード検品のうえ納品書と商品を段ボール箱に入れ替え、自動梱包ラインへ送り出します。合せて56か所のステーション間でプラコン搬送を自在に行う「バーチャルコンベヤ」のような運用方式は完全なオリジナルで、先例もなかったとのことです。では、本システムで「物流ロボットの力を全開させる」条件は何でしょうか? それは断然、この2点。
①作業者の手待ちを最小化すること
②AGVの手待ちを最小化すること(いずれも=稼働率最大化)
まず22か所のデジタルピッキングステーションに配置されたピック作業者に、「AGVが来ないのでピック仕事ができない」という手待ち時間を発生させないことが肝要です。そのための工夫の1つが、AGVは各ステーション脇に「手前から・奥から」の両方向から並び、列につけるようにしたこと(写真8)。ターンとかの動きの制御も細かい。見ていると大体「常時2-3台」のAGVが列について途切れることはほぼなく、作業者の手待ちを回避していました。
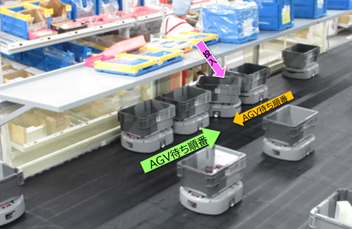
逆に、このステーションにAGVが集中・偏在して渋滞を作ってしまうと、AGVにはムダな待ち時間ができ、他のステーションに行くAGVが減って作業者の手待ちにつながってしまいます。「物量の変動・アンバランスは物流効率化の大敵」とは真理であって、これを防ぐための、「各ピッキングステーションへの商品配置最適化」「ロボット到着タイミングの分散化・平準化」が超重要ポイントになります。約1,100アイテムの商品を販売特性に合わせてバランスよく分散・重複配置し、曜日・月間・季節変動、セールなど販売政策に応じ機動的なメンテナンスをかけ続けること――がマストです。物理的なロケーションだけでなく、その日の作業バッチ編成で、出荷指示データ上で時間的な偏在も防ぎ、バランスよくオーダーを配する必要もあるでしょう。
こうして掘り下げると、「物流ロボットの運用最適化」には、ハードの物理的な話のみならず、運用・ソフト面で大変に奥深い工夫が必要になることが分かります。私は本センターを2度取材して考察を重ね、ようやくその核心に辿り着いた気がします。本事例での運用最適化のカギは、
①センターのオペレーションを担う物流パートナーとして30年以上の経験を重ねた流通サービス社が、オルビス商品の物流特性を知り抜きビッグデータを保持しているから最適化調整が可能なこと
②オルビスの物流センター長がロボットの力を全開させるため、商品配置最適化に週次以上の高頻度で執念のメンテナンスを続けていること
――この2点にあると思い至りました。商品配置最適化・メンテナンス励行は、AMR運用でも完全に共通する「物流ロボットの使いこなしポイント」になります。もちろん、これらは経験の少ないユーザーが自力でやろうとしても、容易なことではありません。周囲に信頼できる外部業者などがあれば、その知見を活用することも一法だと思います。
本システムの設計と構築を主導し、 「作業員約3割削減、1件あたり出荷コスト約2割削減」の成果を生み出したオルビスの前物流リーダーは、ライバル各社の現場見学も受け入れていると聞いて驚く私に、涼しい顔で言いました。「……だって、本当のノウハウは、眼に見えないところにあるから」。
そこで私は、初めて気が付いたのです。そうか! 表面をいくら見たって、内側に長年月積み重ねた苦心のノウハウ、運用ソフトウェアのキモは分からない。いや、見えないのはそれだけじゃない。そのもっと奥にある、中心者の「情熱」、何が何でもロボット導入を成功させるんだ、という「執念」……それこそが「物流ロボットの力を全開!」させた、原動力だったのではないか。
はい?このデジタル/AI時代に、「情熱」「執念」? ……笑い話と思われるかもしれません。それでも私には、「ロボットの力を全開するのは、人の熱い魂だ!」と信じる根拠がもう1つ、あるんです。次回の(事例2)を楽しみにお待ちください。
(※)<参考文献>YEデジタル菊田コラム「未来への道しるべ/物流センター自動化のステップ編(第4回)、
https://www.ye-digital.com/jp/product/mmlogi/column/s01-04.php
鈴与シンワートでは「鈴与グループが持つ物流ノウハウ」と「鈴与シンワートのシステム開発力」を生かし、物流の課題を解決する最適なソリューションを提案します。
お客様の課題に合わせ、デジタルツインなど最新のテクノロジーと知見を活用した物流ITコンサルティングの提案も可能です。是非お気軽にお問い合わせください。
https://www2.shinwart.co.jp/l/907272/2021-11-28/39gg2