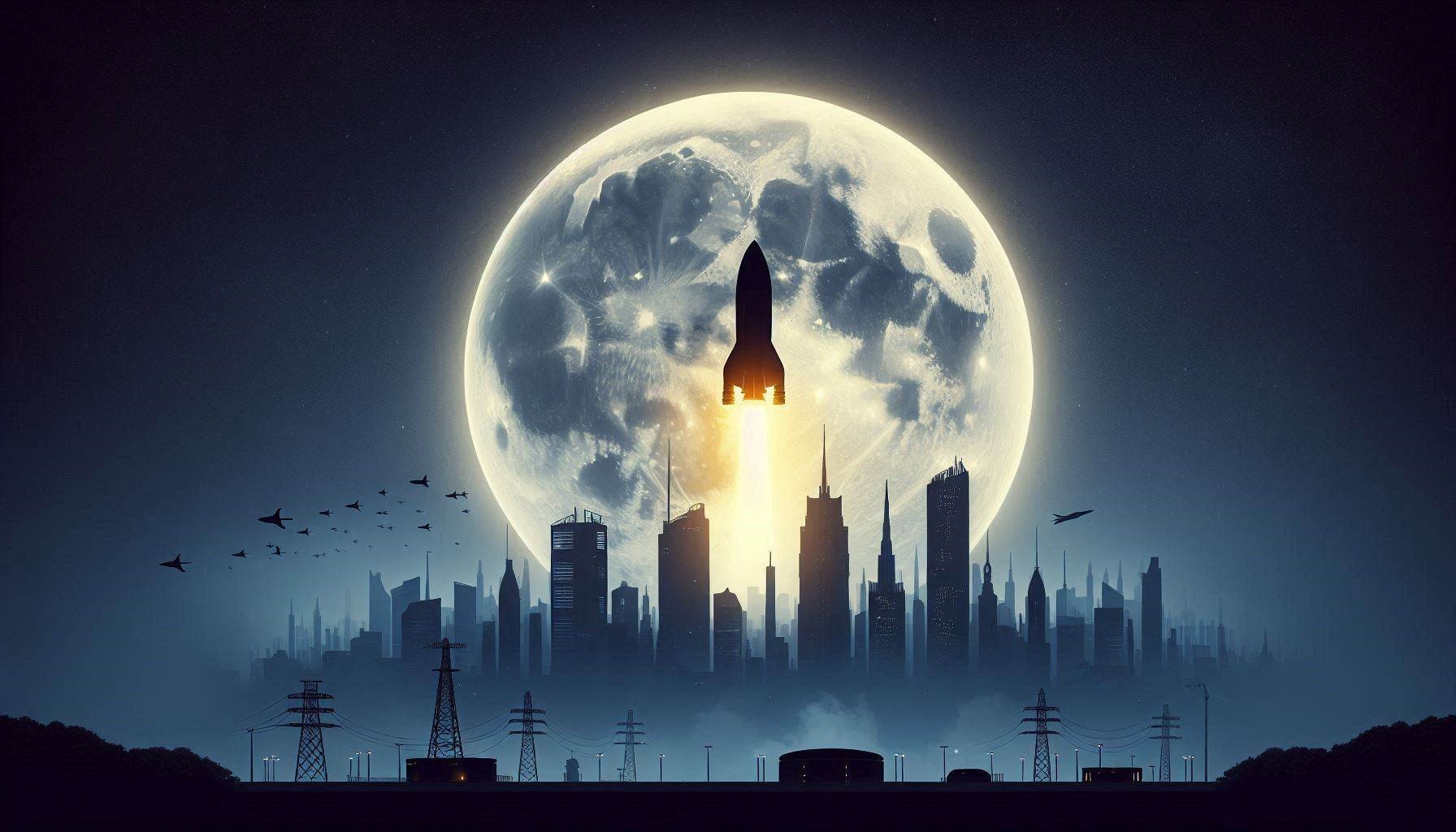
菊田一郎連載コラム
<物流ムーンショット>
Moonshots on Logistics
あるべき物流へ、勇気あるチャレンジを!
*ムーンショット*
前人未踏で非常に困難だが、達成できれば巨大なインパクトをもたらす壮大な計画や挑戦。
月を目指した、あのアポロ計画のように。
<MoonShots-3>
DFL:デザイン・フォー・ロジスティクス!
物流・ロジ効率を最大化する製品・荷姿設計
目次
「積載効率」はなぜ、そんなに重要なのか
最近は物流危機対策が真剣に論じられるようになり、トラックへの「積載効率」というワードを皆さんもよく見かけるようになったのでは?と思います。国交省は積載効率=輸送トンキロ/能力トンキロで算定しており、これが近年は4割を切っています(往復平均で)。つまり日本中のトラック全体でみて「6割が空(カラ)の状態で走っている」ことになり、「トラックが足りないと騒いでいるのに、それはないだろう!」と対策が求められるようになりました。
積載効率を上げるほど一度に運べる量が増えるので、必要な車両台数とドライバー人数が減らせます。トラック便の削減はそのまま、GHG排出削減にも直結します。だから「このままでは2030年にドライバーが21万人も足りなくなる!」と言われる中で、積載効率の向上は有効かつ喫緊の対策としてクローズアップされてきました。では積載効率を高める方策は……?
輸配送での「サプライチェーン階層に対応するユニットロード」単位ごとに、いくつもの手段が考えられます。主なものを挙げましょう(以下の階層区分は図表1のJIS規格による)。
<図表1 サプライチェーン階層と対応荷姿>
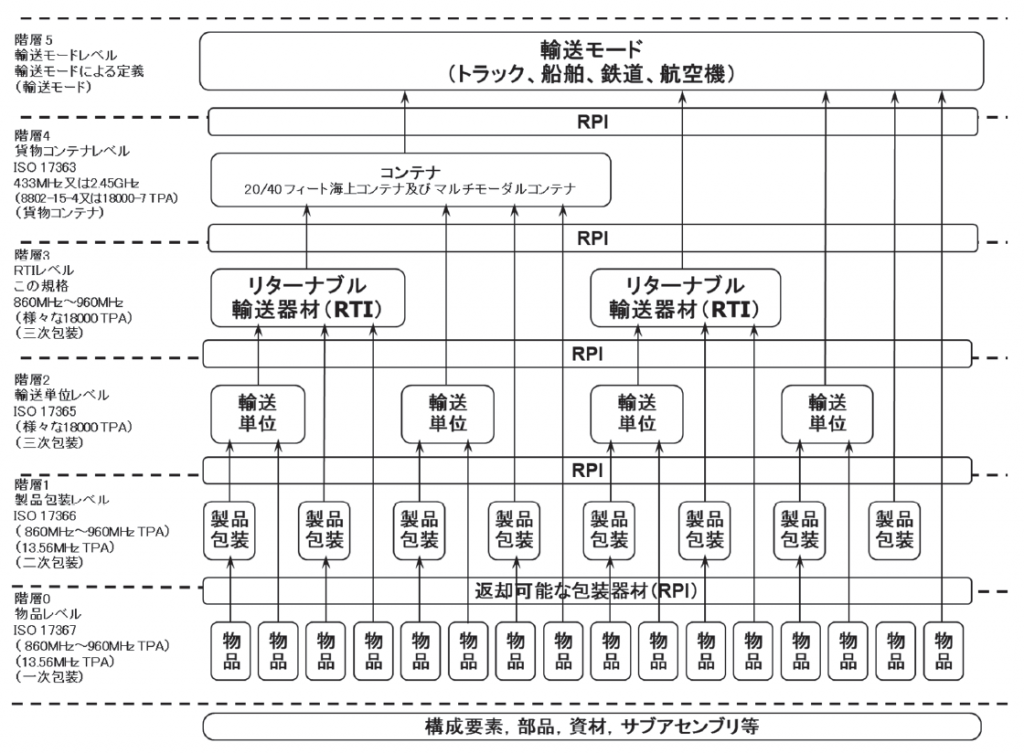
*出典/日本産業規格、JIS Z 0664「RFIDのサプライチェーンへの適用」
積載効率を高める方策~階層別にみる
①階層4,5/輸送モード・貨物コンテナレベル……トラック荷台・貨物コンテナへの積載率
国交省のいう「積載効率」とは、このレベルのトラックへの積載効率を指しています。そもそも低い積載効率のままでもトラックを出し、届けなければならない理由とは……?
・積載率よりも「今すぐ、早く!」のスピードが優先される
・事前に輸配送量が不確定なため予測で手配した車両と合わず、満載にできない
・そもそも生産ロットなど荷物の量が少なく、空いてしまう(車格を落とすほどではない場合)
・パレット寸法と荷台寸法が整合化していないので、隙間ができてしまう
・帰り便の荷物が取れない(泣
……などでしょうか。いずれも物流現場単独でオペレーショナルに=運用で解決できる問題ではなく、他部門・他社との交渉が必要になります。積載効率を高める対策としては以下が思い浮かびます(発側の物流事業者を主語にした場合。皆さんのお立場で読み替えてください)。
👉発着荷主と交渉し、ロットをまとめ、積載効率を高めて出荷できるようにする
👉発着荷主と交渉し、複数荷主の荷物を混載して運ぶ共同物流で積載効率を高める
👉発着荷主と交渉し、納品リードタイムを延長して確定情報での車両手配を可能にする
👉発着荷主と交渉し、トラック荷台に整合した積載効率を最大化できるパレットに転換する
👉営業が頑張り帰り荷を確保する
……以上のように本レベルにおける積載率の向上施策は、基本的に企業間連携・企業内組織連携を要する、サプライチェーン/ロジスティクス階層の「戦略・戦術的課題」となります。
———————————————————————————-
(注)積載効率最優先が既定方針で、パレットを使わず、商品の直積み=手積み・手下ろしで満載にしている例が今もある。荷主と会社が安易な経営感覚で決め、オペレーション階層の現場任せで続けているのだろう。それで積載効率を100%にできたとしても、過酷な手荷役作業をドライバーや現場作業者に今後も強いることが許されるのか。それで人が集まるのか。持続可能性は低く、一刻も早く脱却すべきと筆者は考える。
②階層2,3/輸送単位、輸送機材レベル……パレット、包装箱等への積載効率
「トラック荷台」からサプライチェーン階層を1段降り、荷台に積むパレット(図表1ではRPI/RTI)への、包装箱等の積載効率にも注目しましょう。箱とパレットの寸法が整合化していないためピッタリに積めず、パレット平面の使用比率で1-2割も空いてしまう、などの例も残念ながら「物流あるある」かと思います。
小型商品であればさらに1階層降りて、包装箱となるカートンケースや折り畳みコンテナ(オリコン)などに多数を詰め合わせて「ひと箱」にするときの効率はどうか。箱の寸法と製品寸法が合っていないため容積が余り、積載効率を落とすこともあるでしょう。積載効率はトンキロ数で決まるため、平面積・容積の使用比率は直接の指標になりませんが、より多く積めれば重くなり積載効率は上がるので当然、因果関係はあります。
この輸送単位・機材レベルにおける積載効率向上施策は、何か? つまり「パレット/包装箱への製品の積載効率向上策」に焦点を絞り、以下本文を論じようと思います。筆者がその切り札かつ本質的施策と考えるのが、今回掲げる物流ムーンショット、「デザイン・フォー・ロジスティクス=Design For Logistics:DFL」なのです。
スウェーデンの角砂糖…DFLのベストプラクティス
DFLは本来、建築や製造プロセスも含む広い概念なのですが、ここではDFLを「ロジスティクス効率を最適化する製品・荷姿設計」と解釈して話を進めます。まずは私が伝え聞く「DFLのベストプラクティス」を例示して、この概念のすごさを理解いただこうと思います。その事例とは、「スウェーデンの角砂糖」――であります。
「はあ??」と思われる方も多いでしょうか。でも一昔前の物流畑では、かなり人口に膾炙していました。後継のリーダー各位に語り継ぐ責務が私にはあるので、あえて繰り返しましょう。
これは私が物流の師と仰ぐ、平原直(日本パレット協会創設者の1人、初代会長/敬称略)から生前(主に90年代)、何度も聞いた話で、当時の同門の先輩たちもたびたび書き残している逸話です。今となっては直接のエビデンスがないのですが、以下の筋でご納得いただければと。
平原は物流の社会的全体最適化のため、標準化された荷姿=ユニットロードの単位にまとめて物を運ぶユニットロードシステム化は致命的に重要であり、パレット規格の標準化とそれに整合した輸送荷姿の標準化がいかに有用であるか、語ってやみませんでした。
平原いわく、「(当時からユニットロードシステムの先進国として世界に知られた)スウェーデンでは角砂糖の寸法が、ユーロパレット(大陸欧州で当時も今も約9割の普及率を誇る標準パレット、平面寸法800×1200mm)に最適に積めるよう計算して設計されている。包装箱はユーロパレットに隙間なくぴったり積めるようになっている……」(趣意)
「ユーロパレットにぴったり積める段ボール箱の寸法」とは、物流モジュール寸法の見本として名高い「400×600mm」だったことは間違いありません。これが同パレットには4個、ぴったり積めるのでパレットへの積載効率は100%。さらにこのパレットのトラック荷台への積載効率も、今では100%近い高効率になっているはず。欧州のトラック規格は外寸幅が2550mm以内とされ、平原の生前はまだ内寸幅が2400mmに満たなかったのでユーロパレットを横に2枚積めず、縦横組み合わせて積んでいたようです。しかしその後、厚い側壁を薄いシートシャッターにするカーテンスライダー(サイダー)が有蓋大型トラックの約7割にまで普及し、必要幅を確保できたことで、横に2枚が積めるようになったのです(写真1,2)。日本で普及するウイング車の側壁は欧州のISO規格が定める強度を確保できず、ほとんど使われていないとのこと。私が2000年以降の約20年で数百時間、ドイツほかのアウトバーンをバスで移動した経験でも、有蓋トラックの大半がカーテンスライダー車だった印象です。
<写真1,2 ドイツのカーテンスライダー車両と、パレットにピッタリ積まれた通い箱>
(トラック荷台に幅1200mmパレットを横に2枚ピッタリ積み、その上には400×600mmの飲料用通い箱をピッタリ4個積んでいる)
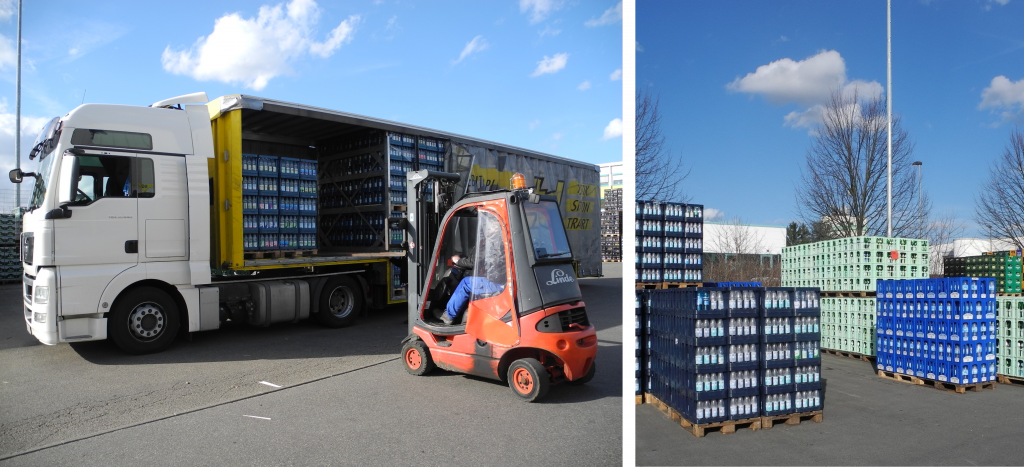
*2015年、ドイツのEDEKA社物流センターで筆者撮影、©流通研究社
「パレットへの積載効率」に話を戻してまとめましょう。
*輸送に使用するパレットは、800×1200mmのユーロパレット(自明の大前提)
*パレットに積む包装箱は、そのモジュール寸法である400×600mm(中前提)
*内箱は段ボール箱にちょうど詰み合わせられるモジュール寸法(不明)で設計
*角砂糖は紙で個装のうえ、この内箱にピッタリ積める整合寸法(不明)で設計
……この理想的なDFLにより、製造以降のサプライチェーン全階層において、箱への/パレットへの/トラック荷台への、積載効率を最大化できています。実は角砂糖に限らず、上の写真にある飲料や牛乳パックなどの加工食品、雑貨他全般にこの思想が貫かれているようです。そのため、倉庫のラックやコンベヤもフォークリフトも、すべてこのパレットと箱の標準寸法を前提に設計され、庫内の保管効率も搬送効率も、それら設備機器の製造効率も、最大化されています。産業界全体の物流、ロジスティクス、製造工程に「標準化とDFLによる積載効率最大化」の原則が貫かれた時、どれほど巨大な社会的利益が得られることか。ぜひ想像してみてください。
スウェーデンで私は見た。角砂糖の現物を…
サプライチェーン全工程で、ユニットロード各層の積載効率を最大化できるのが、DFLのすごさです。その前提は、物流荷姿標準化の要であるパレット寸法が標準化され、社会に浸透していること。「標準パレットが9割」という世界では、可能な限り「あらゆる製品を標準荷姿に整合化した寸法で設計すること」が、ビジネス意思決定の鉄則になります。「角砂糖1個の寸法までがパレットと整合している」と聞くと、我々は「えええっ、そんなにすごいのか!」と驚嘆してしまいますが、この世界の経営者にとっては、整合化させることに余りにも決定的なメリットがあるのだから、誰が考えても当たり前の意思決定だと思います。
たとえばもし、上のユニットロード3階層で積載効率が各80%だったと仮定すると、0.8×0.8×0.8=0.512と、各層合わせた物流・ロジスティクス効率は角砂糖の半分になってしまう。そんな意思決定が許されるはずもなく、経営者は即刻株主から罷免されることでしょう。
こうした「物流荷姿標準化の圧倒的な効果」について、私は学会の先生方に研究し試算してもらえないものかと以前から呼びかけていますが、なかなか見えてきません。ようやく今年の6月に公表された「官民物流標準化懇談会 パレット標準化推進分科会 最終とりまとめ」において、やや近い記述が見つかりました。これは「標準パレット化する」効果をみたもので、前提が若干違うので参考例として見てください。
👉本分科会での試算によれば、標準規格のパレットを標準化された方法で運用することで、現在のパレット化可能な貨物の輸送に係る総作業時間(推計)約7.2 億時間の内、年間約2.3 億時間削減(約32%削減)することが見込まれる。
*引用/「官民物流標準化懇談会 パレット標準化推進分科会 最終とりまとめ」
https://www.mlit.go.jp/seisakutokatsu/freight/content/001751645.pdf
……ところで私はもう1つ、この話を補強する得難い材料をもっています。雑誌の編集長時代、1990年前後に数回、スウェーデンを含む物流現場各所を訪れました。途中からテーマを「欧州のユニットロードシステム」とし、北欧やドイツ、オーストリアなどのパレットシステムを何度か視察する中で、スウェーデン企業を訪問したある日のこと。ミーティングで出された、やたら濃いコーヒーの味も忘れませんが、そのテーブル脇に並べてあった角砂糖を見たら、なんと! まさに師匠の話の通り、ユーロパレットの相似形にみえる縦横比2:3くらいの、平たい直方体だったんです! ああ残念、その場で写真に撮ることも、現物をこっそり持ち帰ることもしなかったのは、今もわが痛恨の一事。だいたい、こんな感じだったんですが……。
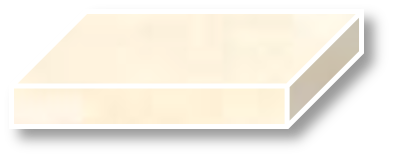
*キクタ作「スウェーデンの角砂糖 1989」
記憶では短辺の幅が15mmくらいだったかと
AIチャットで調べた範囲では、現在の通販商品にはスウェーデン他でも「直方体の角砂糖」が見つからず、キューブの立方体ばかり。他には星形、ハート形とかがあるくらいでした。でもキューブになっても、箱やパレットとの整合設計は保たれているに違いありません。
日本にもチャレンジ事例はある
日本企業にだって導入事例はあり、私も過去に数件を取材しました。古くは2000年代、ルノーとの連合時代の日産自動車が堂々「DFL」を掲げ、海上コンテナに最適効率で積めるボックスパレット寸法を再設計し、それに最適効率で積めるよう部品設計まで調整したという事例をSCM部門の日本トップから聞き、いたく感心しました。
最近の注目事例では、EC大手のアスクルが「飲料水のペットボトル設計を変更し、EC商品の混載梱包ができるよう最適化」した事例が光ります(図表2)。他社でも包装設計の変更でパレットへの積載効率を大幅に向上させた事例が賞を受けたりしています。
<図表2 ペットボトルの設計変更で積載効率を高めたアスクルの事例>
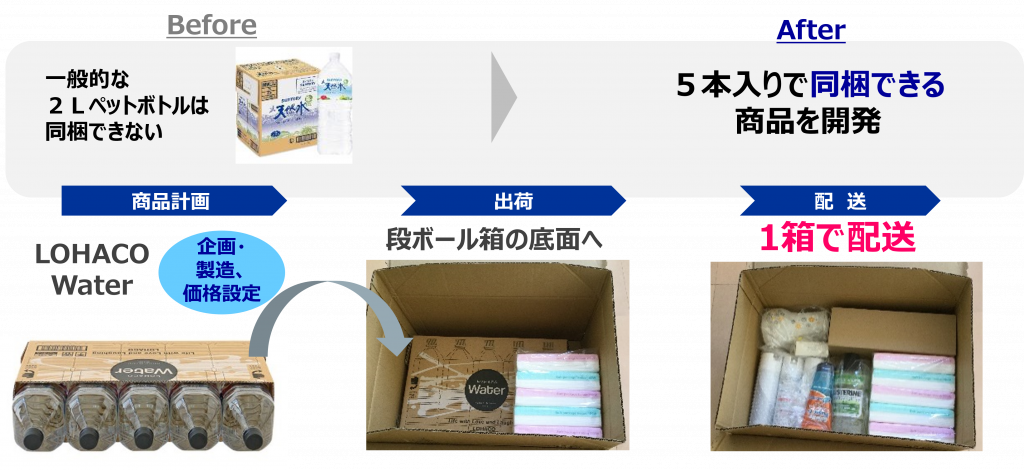
*出典/アスクル提供資料より
DFLを自ら実行できるのはメーカーのほか、PB品をもつ流通業やSPA企業、商社などに限られます。でもDFLのすごさを理解していれば、ロジスティクス全体最適化発想のない荷主に、物流現場の苦労を知り尽くした物流業から提案することだって可能なはず。
最後に、「何のためのDFLなのか」を再確認しておきましょう。DFLの目的は、輸送・積載・保管等の物流・ロジスティクス効率を最大化して生産性を高めると同時に、人の労務環境と地球環境を改善し、物流と産業社会の持続可能化に寄与すること――私はそう考えます。
より多くの関係者がこのムーンショットに挑み、「DFL思想」が日本企業の経営の根幹に根付くことを、私は心底、期待しています。
(参考文献)
Japan Innovation Review菊田コラム「物流ミライ妄想館」⑤、荷姿標準化の理想形、ドイツ最大スーパーが堅持するユニットロードシステム
https://jbpress.ismedia.jp/articles/-/80548
鈴与シンワートでは「鈴与グループが持つ物流ノウハウ」と「鈴与シンワートのシステム開発力」を生かし、物流の課題を解決する最適なソリューションを提案します。
お客様の課題に合わせ、デジタルツインなど最新のテクノロジーと知見を活用した物流ITコンサルティングの提案も可能です。是非お気軽にお問い合わせください。
https://www2.shinwart.co.jp/l/907272/2021-11-28/39gg2